Introduction to Denroy Ltd
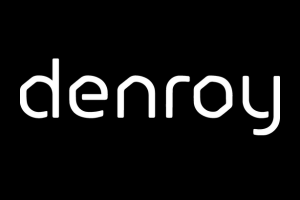
Welcome to Denroy Ltd!
As a world leading innovator in the design and manufacture of engineered polymer components & solutions, we would like to introduce ourselves to anyone coming to our website for the first time or to people who would like to know a little more about us.
Denroy Limited is a leading injection moulding manufacturer with over 50 years’ experience and expertise in research and technology, design, prototyping, manufacturing and quality assurance, for supplying precision industries such as Medical, Aerospace, Defence, Automotive, Commercial and Brushes.
Based in Northern Ireland, and still a family owned business, Denroy was founded in 1972. The Group consists of three brands: Denroy, Denman (haircare) and DenPro (medical).
You may be most familiar with Denroy’s sister company, Denman but what you may not know is that Denroy has been responsible for manufacturing these iconic British made hairbrushes for over 50 years. Denroy has a hugely diverse list of products we manufacture, including plastics components used in fighter jets, passenger planes, forklift trucks, medical devices and over 100 other applications.
The Denroy Group operates over 2 main sites and recently dramatically increased the overall factory footprint with a new manufacturing facility extension. A new distribution centre was also built as an additional warehousing and materials storage facility.
During a re-structuring in 1995 Denroy took over all injection moulding from British Aerospace, seeing the company start supplying major programs such as Airbus A320, Hawk and Tornado.
This was just the beginning of Denroy’s relationship with the aerospace industry and in 2014 Denroy worked with Bombardier when the C-Series (now Airbus A220) was being developed to replace small – to medium-sized machined aluminium and titanium brackets for wings, center wing-box and fuel-tank applications, intended to last the life of the aircraft despite constant immersion in fuel.
We have recently signed a collaborative research agreement with Airbus to work on the Wing of Tomorrow which will see Denroy apply its expertise in plastics and composite component design and manufacturing to deliver innovative components for application on the Wing of Tomorrow demonstrator.
Our capabilities in high performance, engineering thermoplastics make Denroy an ideal partner for components for various structures and systems across the aircraft. We specialise in lightweighting and metal replacement and currently supply parts for wings, nacelles, fuselage and propulsion systems.
Our expertise with colours, gloss finishes, textured finishes, printing and painting allow Denroy to work with their customers to meet the high expectations of the aerospace interiors market. We have capability in high temperature polymers such as Polyetherimide (PEI) & Polyphenylene sulfide (PPS), as well as flame retardant materials to meet FR requirements for interior components.
In the automotive sector we are always looking to light weight components, helping to assist in more fuel-efficient and environmentally friendly final products. Our design team partner closely with the Original Equipment Manufacturer (OEM) and end users to ensure the best product is manufactured.
With on-site design systems, tooling facilities and injection moulding machines ranging from 5 to 900 tonnes, including twin shot moulding, the Company is perfectly positioned to assist all customers in getting product to market at competitive prices.
As an ISO9001 accredited company, every product, no matter what the sector, must pass exacting quality standards in the production environment to ensure complete customer satisfaction. The use of robotic equipment and in-house data collection systems ensures repeatability during the moulding process and helps control product costs.
Denroy prides itself on being a single source solution from concept design to full volume production offering an integrated design, tooling, and manufacturing operation.
With Denroy’s expertise we can take products from concept through design, development, prototyping and testing, and finally to manufacturing, finishing, assembly and quality assurance.
Design
Our design team works in close partnership with clients to develop initial design concepts or to take existing designs and make them suitable to manufacture via the injection moulding process.
Our design capability includes 3D CAD packages such as CATIA and Pro-E along with the material simulation package Moldflow Analysis. The use of the various design packages enables Denroy to identify potential risk areas at an early stage in the design process thus reducing the product time to market and avoiding costly mistakes in tooling manufacture. The use of on-site 3D prototyping machines further enhances the company offering to the final customer.
Typical product development processes would include:
– Initial Concept Generation
– Creation of 3D models
– Assistance with raw material selection
– Simulation of the Moulding Process
– Prototyping
– Creation of detail drawings
– Project management and procurement of mould tools
– Tool trials
– Full Volume Production
Research & Technology
We work with partners in industry to develop new and innovative processes, concepts and components for complex aerospace and defence applications.
They invest heavily in research and development to ensure we remain at the forefront of thermoplastics technology. Most of our R&T activities fall into the following key areas:
Hybrid Moulding / Composite Overmoulding
We have industry leading capabilities in moulding thermoplastics composite components with injection moulded features such as bosses, ribs or embedded components. Again, our aim is to help our customers achieve a high rate manufacture of complex composite components whilst also cutting weight and cost.
Advancements in high temperature, engineering thermoplastics and thermoplastics composites
Our R&T and Design departments work with partners in industry to develop new and innovative processes, concepts and components. Our aim is to take cost and weight out of aircraft and enable high rate manufacture of complex aerospace and defence applications. Partners we are working with in these areas include Airbus, Boeing, Bombardier and Thales.
3D Printing / Additive Manufacture
As a highly experienced plastics supplier to high tech industries such as Aerospace, Defence Automotive and Medical, we are the ideal partner for 3D printing research and development projects. We are working with aerospace primes and tier 1s as well as with commercial brands like our sister company Denman to advance plastics 3D printing technology. Our additive manufacturing capabilities allow them to print high temperature plastics such as Polyether ether ketone (PEEK), Polyetherketoneketone (PEKK) and Polyetherimide (PEI) as well as commodity plasticS grades. They have both stereolithography (SLA) and fused deposition modeling (FDM) machines with a range of size capability meaning we can cater for a wide variety of applications.
Prototyping
Denroy has advanced capabilities in 3D printing thermoplastics.
They have SLA and FDM printers and can make parts in various materials and sizes meaning they can cover a huge variety of applications. Materials they can print include the following:
– Polyether ether ketone (PEEK)
– Polyetherketoneketone (PEKK)
– Polyetherimide (PEI)
– Polyamide (PA) (Nylon)
– Polylactic acid (PLA)
– Acrylonitrile Butadiene Styrene (ABS)
– Thermoplastic elastomer (TPE)
As well as 3D printed prototypes, we also machine prototypes or work with our prototyping partners to produce vacuum cast prototypes. We can produce prototype tooling for products that are in the development phase.
Manufacturing
With investment plans in place, Denroy continues to increase capacity and capabilities throughout the business, including new machining centres, Engel injection moulding machines and a white-room facility.
We aim to increase the scope of their manufacturing processes by increasing our market share in the polymer processing sector. While working with industrial and academic partners, we aim to increase our capability to innovate, increase productivity and enhance the skills of the work force, ultimately strengthening our world class offering. We collaborate closely with universities, material suppliers, industrial bodies and partners to remain at the forefront of manufacturing techniques.
Our comprehensive manufacturing facility uses state of the art injection moulding equipment encompassing the latest software for process set-up and repeatability.
With machines ranging from 5 to 900 tonnes, we can produce components weighing from a few grams up to 4.5 kilos in a wide range of materials including the commodity polymers to the high-grade engineering polymers such as PEEK, PEI and PPS.
We have a centralised vacuum material feed system and are continuing to invest in robotic handling equipment ensuring consistent manufacturing cycling providing the highest quality product for our customers.
Quality
Our continuous improvement initiatives, process monitoring equipment and purpose built MRP system help to minimise waste, reduce manufacturing lead times and ensure quality product every time.
Denroy are one of only four companies worldwide to hold the ADS 21st Century Supply Chains Gold Award. Even more impressively we are one of two companies to retain the award for 6 years in a row.
Current areas that Denroy’s R&T department are working on include: Hybrid moulding and Overmoulding: Thermoplastics composites: Thermoplastics welding and joining: Advanced 3D printing.
Our focus is on delivering solutions and innovation in everything we do, through the strength of our people.
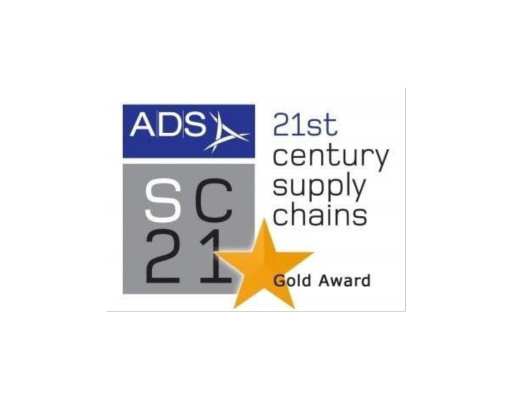
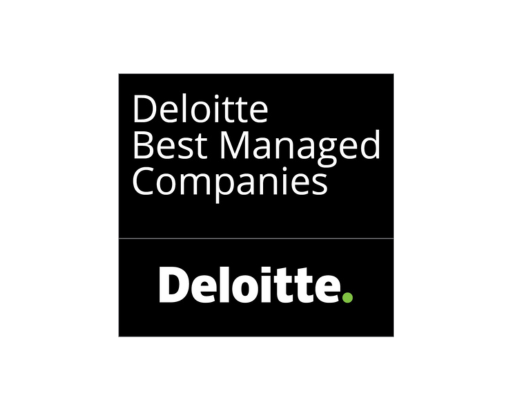