Lightweighting
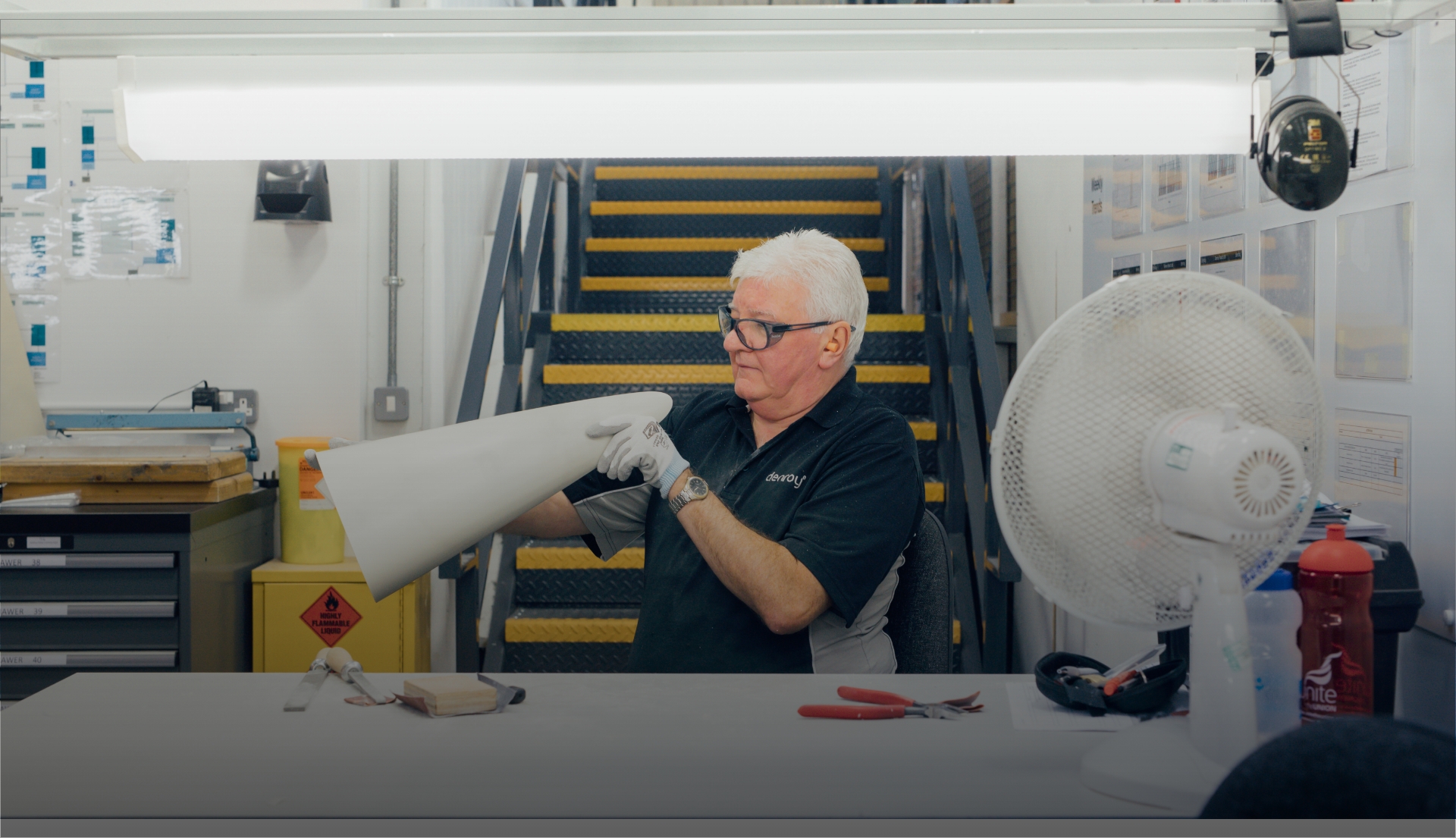
Did you know that Denroy are a world leading innovator in the design and manufacture of engineering polymer components and solutions?
Specialising in high temperature polymers for metal replacement has given Denroy the opportunity to collaborate closely with Bombardier and Victrex to replace small – to medium-sized machined aluminium and titanium brackets for wings, center wing-box and fuel-tank applications on the C-Series (Airbus A220). VICTREX PEEK is intended to last the life of the aircraft despite constant immersion in fuel. It also complies with lightning strike requirements, and is resistant to wear and aggressive aerospace fluids.
But what are the real reasons for using Denroy’s expertise in this area?
Unlocking the Power of Light Weighting in Aircraft Interiors.
Light weighting is revolutionising aircraft interiors, making it amongst the highest priorities for the aerospace and automotive industries.
The benefits are huge that come with this game-changing approach. Such as:
~ Enhanced Fuel Efficiency
~ Increased Passenger Comfort
~ Expanded Cargo Capacity
~ Improved sustainability
~Streamlined Maintenance
~ Innovative Design Possibilities
Weight reduction can have enormous effects on the efficiency of an automobile or aircraft. A reduction in weight directly results in a reduction in fuel usage, therefore a reduction in costs economically and environmentally.
In the past some metals like aluminium have been used in the lightweighting process, but the high porosity of lightweight metals could produce unreliable parts. Composite plastics, however, can be engineered to meet the needs of the environment they will function in, by developing custom-engineered resin to stand up to harsh conditions ranging from saltwater to chemicals to extreme heat and pressure. This keeps all the benefits of lightweighting while avoiding the risks of certain metals from public products.
Several metal parts can be redesigned using the freedom of plastics injection tooling to create a single plastics part which again reduces weight and transportation costs.
And finally labour costs are reduced due to plastics parts often being produced quicker and more efficiently.
As Denroy is an ISO9001 accredited company, you are not just getting a lightweight solution but peace of mind. Every product must pass exacting quality standards to ensure complete customer satisfaction. The use of robotic equipment and in-house data collection systems ensures repeatability during the moulding process and helps control product cost in this price sensitive market.
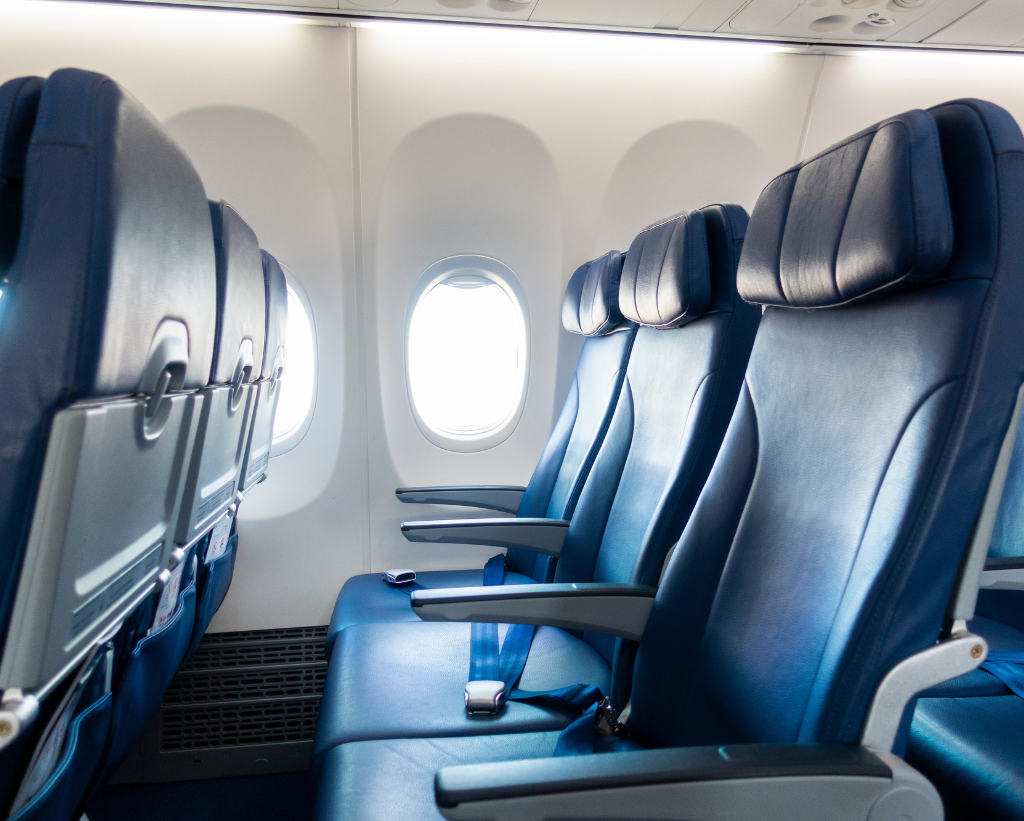
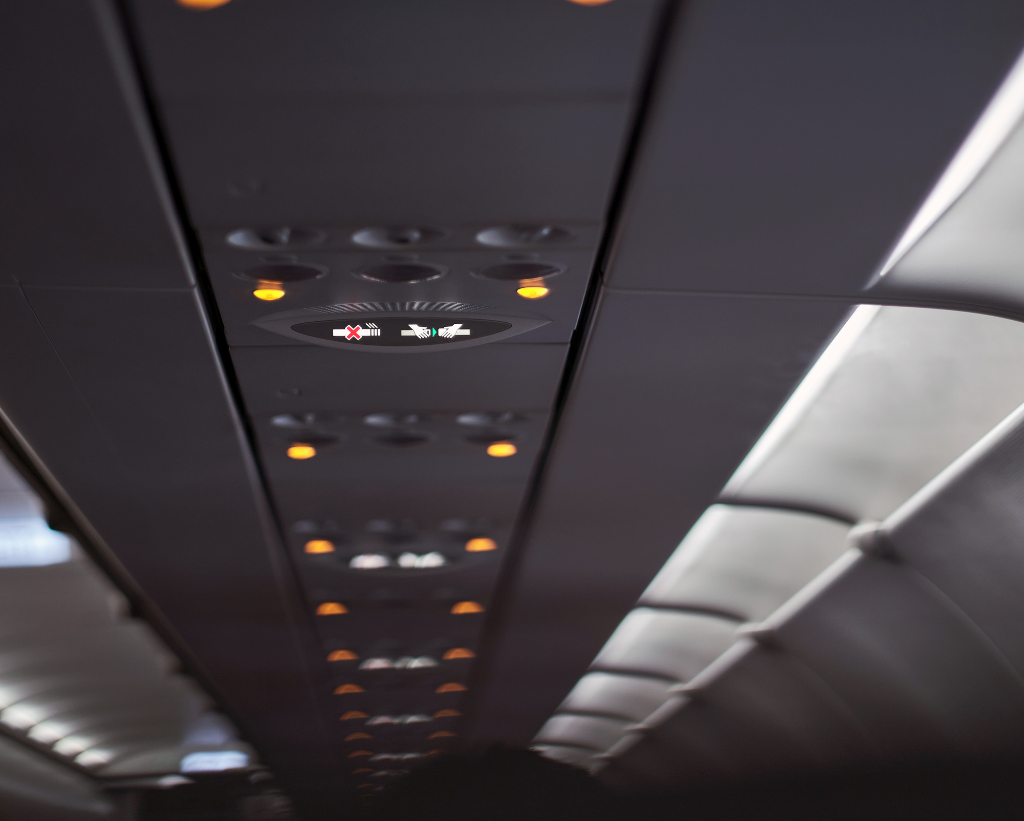
Denroy service a broad spectrum of OEMs in both civil and defence including Airbus, Boeing and Bombardier and in the automotive sector.
We are currently supply parts for wings, nacelles, fuselage and propulsion systems in aircraft and Steering Column Covers, Under Hood Engine Components, Fuel Cell Battery Trays, Cover Fasteners and Plugs and Control Handles with electrical harness in the automotive sector.
We have extensive knowledge and expertise in processing a diverse range of materials, from the most common commodity polymers to the high engineering polymers such as PEEK and PPS.
Our capabilities in high performance, engineering thermoplastics make Denroy an ideal partner for components for various structures and systems across the aircraft.
Our expertise with colours, gloss finishes, textured finishes, printing and painting allow Denroy to work with our customers to meet the high expectations of the aerospace interiors market. We can also supply flame retardant materials to meet FR requirements for interior components.